In a number of industrial facilities, including wastewater treatment plants, mines and refineries, pumps play a key role in ensuring efficient movement of fluids and materials. However, pumps can be hampered by the presence of sludge in the pumped media. In this article, we will look at the effects of sludge parameters on pump performance and efficiency.
Sludge particle size
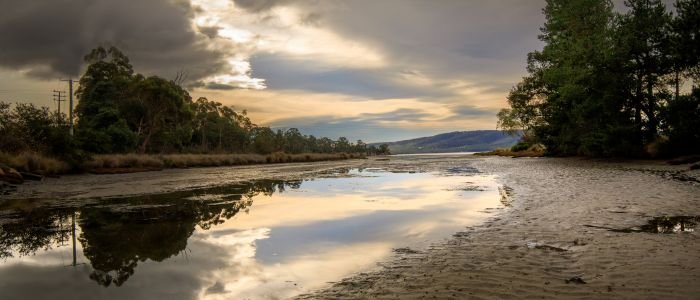
Sludge particle size is one of the important parameters that affects pump performance and efficiency. Depending on the particle size, pumps can encounter various problems affecting their performance and efficiency.
For optimal pump system performance, it is important to select the right pump for the size of the slurry particles. Some pumps are specifically designed to handle larger particles and have stronger components that can handle abrasive materials. Other pumps can be effective at pumping fine slurries by using filtration systems or special designs that prevent clogging.
t is also important to note that the particle size of the slurry can change during the operation of the pumping system. Therefore, regular maintenance and monitoring of sludge parameters is an integral part of ensuring efficient pump operation. This allows timely response to changes in particle size and appropriate measures to prevent possible problems and reduce the negative impact of particle size on pump performance.
Sludge concentration
Sludge concentration determines the amount of solids present in the fluid medium and can have significant effects on the function of the pumping system.
Higher concentrations of sludge can cause clogging in the pumping system. As solids pass through pump passages and piping, they can deposit on surfaces and form deposits. These deposits can cause narrow throat or complete clogging, resulting in reduced flow capacity and increased resistance to flow. As a result, the pump requires more energy and time to pump the sludge, which reduces its efficiency and performance.
In addition, higher concentrations of sludge can cause pump overloading. The large amount of solids in the fluid requires extra effort from the pump to build sufficient pressure and overcome flow resistance. This can lead to unnecessary wear and tear on pump components, increased motor load and reduced pump life.
The optimal solution is to maintain an optimal concentration of sludge in the pumping system. Regular cleaning and maintenance of the pump, as well as the use of additional filters and separators, can help keep the sludge concentration at an acceptable level. This prevents clogging, ensures proper fluid flow through the pumping system, and reduces wear on pump components.
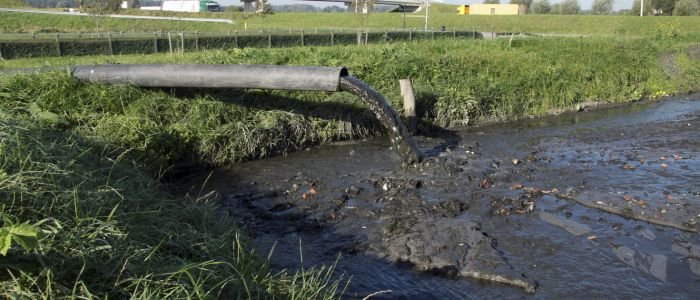
Slurry viscosity
Viscosity determines the slurry’s resistance to movement and its ability to flow. The higher the viscosity of the slurry, the more force is required from the pump to pump the fluid.
Slurry with high viscosity creates additional resistance in the pumping system. Moving a high viscosity fluid requires a more powerful motor or pump with higher horsepower to create enough pressure and ensure normal flow. This can lead to increased energy consumption and higher operating costs.
Moreover, slurry with high viscosity can also cause clogging problems and slow flow in the pumping system. Viscous fluid has a greater tendency to form clogs and deposits on the internal surfaces of the pump and piping. This can result in reduced system flow capacity and reduced pump performance. In addition, deposits on pump surfaces can lead to component wear, shortened service life, and the possibility of failure.
It is important to note that sludge viscosity can vary depending on various factors such as temperature, water content, and sludge chemistry. Therefore, regular monitoring of sludge viscosity and selection of pumps with these parameters in mind is essential to ensure efficient pumping and minimize potential problems associated with viscous sludge.
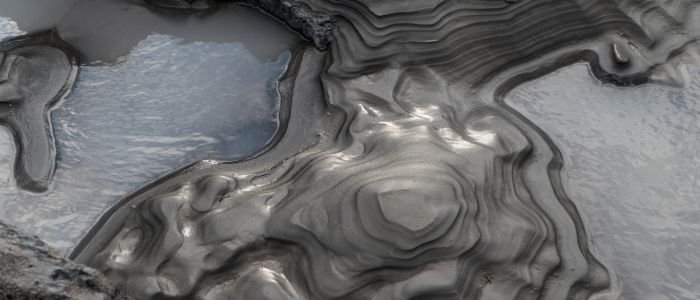
Aggressiveness of slurry
The aggressiveness of the slurry is an important parameter that has a significant impact on pump performance and efficiency. It determines the chemical activity and corrosiveness of the slurry that is pumped through the pumping system.
Aggressive slurry can cause corrosion and damage to pump components. If the slurry contains chemicals such as acids or alkalis, they can react with pump materials, causing corrosion and wear. Corrosion can cause the pump to leak, reduce performance, and even break down. Therefore, it is important to choose pump materials that are resistant to corrosive media and to regularly inspect pump components for corrosion and damage.
Various strategies can be used to minimize the effects of corrosive slurries on pump performance. These may include selecting pumps with materials that are resistant to corrosion and chemical attack. Chemical protection, such as adding corrosion inhibitors to the sludge or applying special coatings to the surfaces of pump components, can also be applied. Regular maintenance and monitoring of the pump also allows for timely detection and correction of problems associated with corrosive slurries.
Conclusion
Slurry parameters such as particle size, concentration, viscosity and aggressiveness play a significant role in pump performance and efficiency. Choosing the right pump, regular maintenance, and monitoring slurry parameters are important measures to optimize pump system performance and extend pump life.
The design and operation of pumping systems should consider these factors to ensure efficient and reliable pump operation in the presence of sludge.