If you’re looking for the best slurry pump, will you address the need for heavy operations? Kingda has something to offer. The slurry pumps that Kingda sells are not just suitable; they are the best.
Kingda is growing to be the largest company in the world that makes and sells high-performance pumps for mining and mineral operations. Kingda slurry pumps are the best for dredging, tunneling, and water treatment functions.
Stay tuned! because this post is for you. It will provide rich information about slurry pumps.
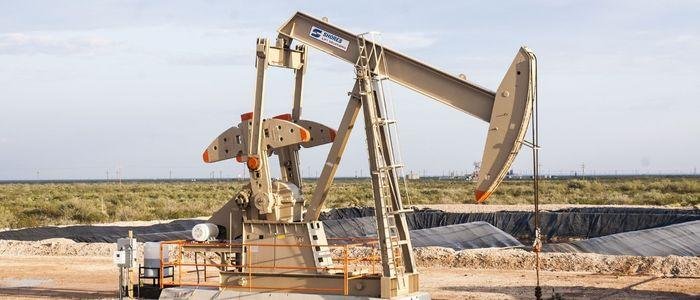
What does “slurry pump” mean?
A slurry pump is a centrifugal pump that moves solid particles that are rough and often corrosive.
Depending on the application, the parts of a slurry pump that come into contact with the medium being pumped are made of wear-resistant metals.
Superior dependability with Kingda slurry pumps High-quality Kingda slurry pumps is perfect for mining, metals, fertilizers, and any other job like removing abrasive fluids.
The optimized hydraulic design has high-efficiency impellers and large casings that make it easier for the slurry to flow.
It means that the pump uses less energy and has a low total cost of ownership. All the pump parts that touch the fluid are made of high-quality, interchangeable metal alloys or materials.
Large cross-sections have a longer wear life, and the wear life can be even longer if the glands sealing options include a dynamic seal and single or double mechanical seals.
Applications for a Slurry Pump
Throughout the process, these systems typically require the movement of large volumes of slurry. Ash disposal from thermal power plants is a common application for slurry pumps. Other slurry pumps’ applications include
- producing fertilizer,
- land reclamation,
- mining by dredges, then
- transporting coal and
- minerals long distances.
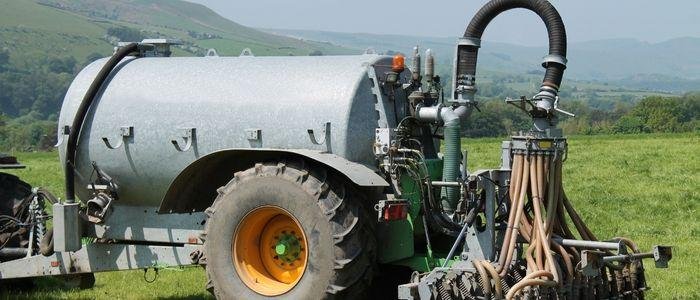
In the future, slurry pumping will be used for many more things. This is because the world is paying more attention to energy and environmental issues.
There are numerous different types of pumps used for pumping slurries.
Like Venturi slurry., positive displacement and particular effect types are used, but centrifugal slurry pumps are the most common.
Centrifugal slurry pumps, like centrifugal pumps for clear liquids, use the centrifugal force made by a rotating impeller to send energy to the slurry. Centrifugal slurry pumps have to consider the size and shape of the impeller, how easy it is to maintain, the type of shaft seal used, and the This is to stand up to rough conditions, eroded, and often attacked. The centrifugal slurry pump must be constructed to allow the passage of abrasive particles that might sometimes be incredibly big.
Slurry Pump Design Features
A slurry pump comprises a pump and a drive, which in construction is often an electric or diesel motor. Slurry pumps have to be designed uniquely because of the high concentration of solids in the medium they move and how they wear down the pump parts. Taking out big things like rocks and pebbles from the pump’s internal cross-section makes it work better.
arranged a series of blades.
When the impeller turns, it creates a negative pressure in the middle, which pulls in the material being moved. Hydraulic fluid comes in through the inlet pipe and is sent to the impeller. Each slurry particle is hit by centrifugal forces and forced into the pressurized discharge line.
Slurry Pump for Particle Erosion
The slurry pumps’ components are subject to excessive hydro abrasive, cavitational, and mechanical wear. A slurry pump’s flow path wear is primarily caused by hydro abrasive impact. Its intensity is affected by many things, including the slurry or particles in the materials being moved and the resistance of the flow path parts to wear.
Hydro abrasive wear can be both local and widespread. It is typical for the surfaces of armor disks, side, radial liners, and pipes to exhibit a relatively uniform thinning due to general wear. Vortex and cavitation regions are subject to a much more intense localized wear than the overall surface.
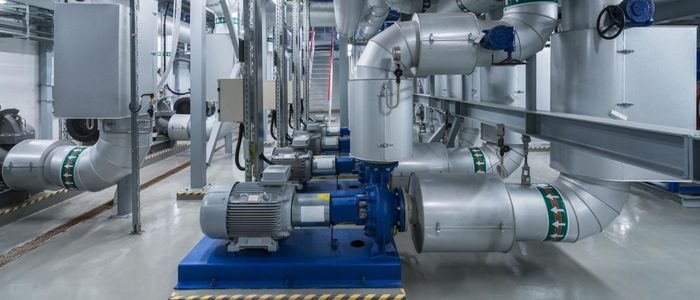
Cavitational Wear
Most of the time, cavitational wear stops a pump from working and causes a vacuum to form in the suction line.
Uneven connections between parts, high spots from electric welding, and worn surfaces cause cavitation. This makes the pump vibrate more and wears out all of its features, including the drive shaft, support bearings, and foundations. To reduce the effect of cavitation, ejectors are installed in drag heads.
Over time, friction and the impact of rocks in the fluid on the slurry pump parts wear them down. This is typical when working with pebble-rich soils. Any wear has a detrimental effect on the pump’s characteristics, reducing output by 20 to 30 percent, and necessitating immediate repair.
Each component of a slurry pump experiences its predominant form of wear. The slurry pump is ordinary gray iron. Rubber-lined slurry pump parts, known as gums, are one of the upcoming trends in the development of slurry pump design. But rubber can’t handle being hit by big pieces, so rubber-lined slurry pumps should only be used with fluids with small solids. But rubber can’t handle being hit by big pieces, so rubber-lined slurry pumps should only be used with liquids with small solids. In general, the following procedures are advised to reduce slurry pump wear:
- Improvement of hydraulic flow conditions in the lines of slurry pumps
- Protection of slurry pump gaps from solids penetration
- Improvement of wear-resistant properties of pump part materials
- Use of protective liners
- Modification of design solutions in slurry pump engineering
Why Choose Kingda in Purchasing Your Slurry Pump
These are the reasons why we think of Kingda as a slurry pump.
You can find the best choice with Kingda by considering flow rate, pressure, work, and efficiency. The feed rate is significant for slurry pumps. When the feed rate is optimized, the pump will last much longer and use less energy.
The concentration and size of solids also affect how long the flow path of a slurry pump will last. The amount and length of solids also affect how long the flow path of a slurry pump will last. Depending on how the slurry flows, the flow systems of slurry pumps will wear differently due to abrasive wear.
Universal regulatory documents for pumping equipment handling media contaminated with solid inclusions in use. A complete process calculation that considers all factors is usually challenging.
Tips for Maximizing Kingda Slurry Pump Efficiency
The demand for slurry pumps is rising in coal, copper, iron ore, phosphate, and other global mines. Kingda has the most technologically advanced and reliable slurry pump in terms of performance, wear resistance, uptime, and total cost of ownership.
Mills and crushers in the modern mining industry are much bigger than in the past. This is because they must process more material to get the same amount of ore. Kingda mill inclines are designed around modern-sized mills to accommodate typical flows efficiently.
Keeping in mind that the needs of the industry are always changing, the Kingda series of slurry pumps are best for highly abrasive slurries in grinding mill circuits and have very high uptime.
The kingda slurry pump series has been designed for efficient operation and the most extended wear life. The series is made with cutting-edge wear technology and has great resistance to wear and erosion.
From kingda.com. We guarantee that you will always be able to find the right slurry pump to meet your process needs because we have the best pump ratio in the industry, a wide range of sizes, and varied uses. Visit our page now.